Warehouse layouts strategy, due to their influence on total warehousing costs, are of interest to the theory and practice of warehouse design.
While the layout problem of the unit-load storage area of conventional warehouses has quite a long history, the layout of conventional systems with manual order-picking from multiple aisles has been the topic of a number of research papers only in the previous decade.
The research has resulted, among other things, in various strategies for optimal layout design. Moreover, some new innovative layouts for storage areas have been proposed recently.
These layouts result in a reduced travel distance needed to store or retrieve a single pallet, thus improving the efficiency in the storage area.
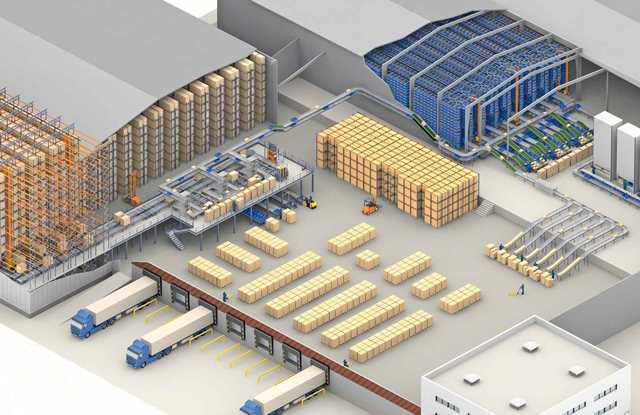
Warehouse layout optimization
However, the question of whether these layouts could perform better than traditional layouts in manual order-picking operations has remained unanswered.
This provides a short overview of optimal traditional layouts of the storage and order-picking area as well as new innovative storage area layouts, followed by results of the analysis of order-picking in these new innovative layouts and relevant conclusions.
The importance of the warehouse in the supply chain network is increasing. The competitiveness of a company is directly influenced by its ability to achieve efficiency in terms of a high rate of on-time deliveries without defects in its supply chain network.
Warehouse layout best practices
Supply chain efficiency and best practices are to a large extent determined in its nodes. In today’s business climate there is a trend towards more product variety and shorter response times.
This puts increasing pressure on warehouse performance in terms of storing articles and the ability to assemble customer orders. The warehouse performance is largely determined during the design phase of the warehouse layout.
It is acknowledged that warehouse layout design is a highly complex task primarily because the warehouse performance affects, and is affected by, other functions within a company’s ability to operate adequately as well as ensure the company’s competitiveness.
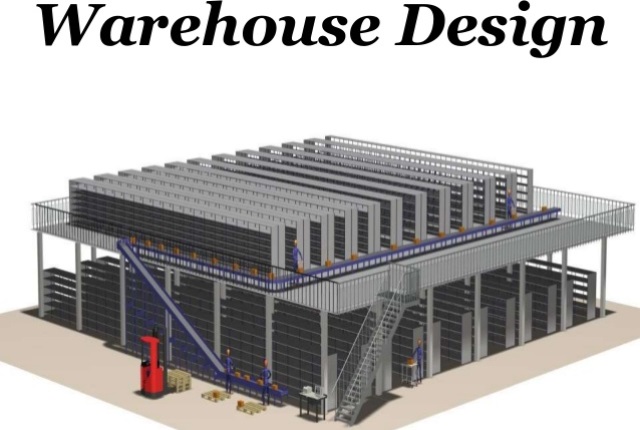
Warehousing and storage services
For this reason, warehouse services have many stakeholders. Additionally, it may be the only view that end customers have of the company’s operational capabilities. Many aspects need to be considered when designing a warehouse both within the warehouse operations and the company’s supply chain network as a whole.
These aspects consider both the nature of the business in terms of customer requirements and demand patterns such as seasonality as well as the characteristics and requirements of the product.
The degree of complexity of warehouse design is largely determined by the number of activities and parallel processes that are performed in the warehouse.
Warehouse layout design example
Warehouse design is fixed in nature as it is often expensive to change after implementation.
Both due to high investment costs in new facilities, racks and equipment, and due to opportunity costs for downtime in operations.
A warehouse normally operates on an everyday basis. A redesign that requires shut down of departments in the warehouse is not an option for many companies.
High costs derived from lost sales, use of a third-party logistics provider or lost production rate can cost more than the warehouse investment itself.
For this reason, it is important for companies that are acting in volatile or fast-moving industries or for some other reason are expecting considerable changes in demand to consider flexibility in their design process.
Factors to consider in warehouse layout
This is to ensure a successful warehouse design solution that is aligned with the company strategy for the life span of the investment.
The requirements and expectations for the warehouses’ abilities are changing.
Is it old-fashioned to see storage as a non-value-adding activity?
Trends in supply chain management such as supply chain integration and supply chain postponement have led to that more value-adding activities are performed within warehouses.
Besides storing and distribution other activities such as repacking and final assembly of products have been introduced to the warehousing service portfolio.
Warehouse design considerations
To support the design process of warehouses, researchers have formed frameworks. Most frameworks reviewed are based on literature reviews and are yet to be tested in practice while others are developed with the help of experienced practitioners and relate loosely to academia.
The availability of frameworks covering the whole design process, from purpose identification to evaluation, is limited in current research and there is a need for further research that connects practice with theory.
However, problems related to warehouse layout design are seldom well-defined and cannot be reduced to multiple isolated sub-problems.
This means that warehouse designers need a mixture of creativity and analytical skills to handle the complex interactions between warehouse activities, future demand, and space requirements.
Questions to ask about warehouse operations
Designing a warehouse is an intricate process with many trade-off decisions to be made between conflicting objectives. The complexity of the process is further increased by the high number of feasible design solutions.
Warehouse design is fixed in nature as the investment cost for the redesign is considerable.
To ensure satisfying warehousing performance during the life span of the warehouse it is important to take the corporate strategy and growth expectations into consideration during the design phase.
The purpose of the study is to develop an aligned warehouse design solution for current and future operations considering a company’s growth expectations. The literature review made it evident that a method to generate a layout design that incorporates future operations in an adequate way is needed.
The following research questions are investigated and answered in the thesis:
What aspects should be considered when designing a warehouse layout to ensure that it is aligned with the company’s growth expectations?
How can a warehouse layout design be generated that ensures flexibility and ability to handle future warehouse operations?

Types of Racks in Warehouse
Racking is much more than just steel. Racking is the key to optimum throughput efficiency because the efficiency of the entire material flow is optimized only through the requirement-specific design of a racking system.
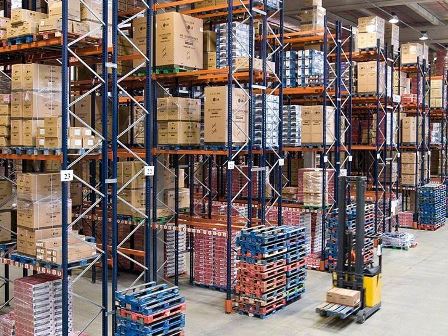
Storage Pallet Racking
Every company faces unique situations when considering its warehouse storage and design options.