The warehouse process, as one of many logistics processes, currently holds an irreplaceable position in logistics systems in companies and in the supply chain. The proper function of warehouse operations depends on, among other things, the type of the used technology and its utilization.
This article is focused on the design of a warehouse system. The selection of a suitable warehouse system is a current research topic as the warehouse system has an impact on warehouse capacity and utilization and on the speed of storage activities.
The post presents a warehouse system design methodology that was designed applying the logistics principle-systematic (system) approach.
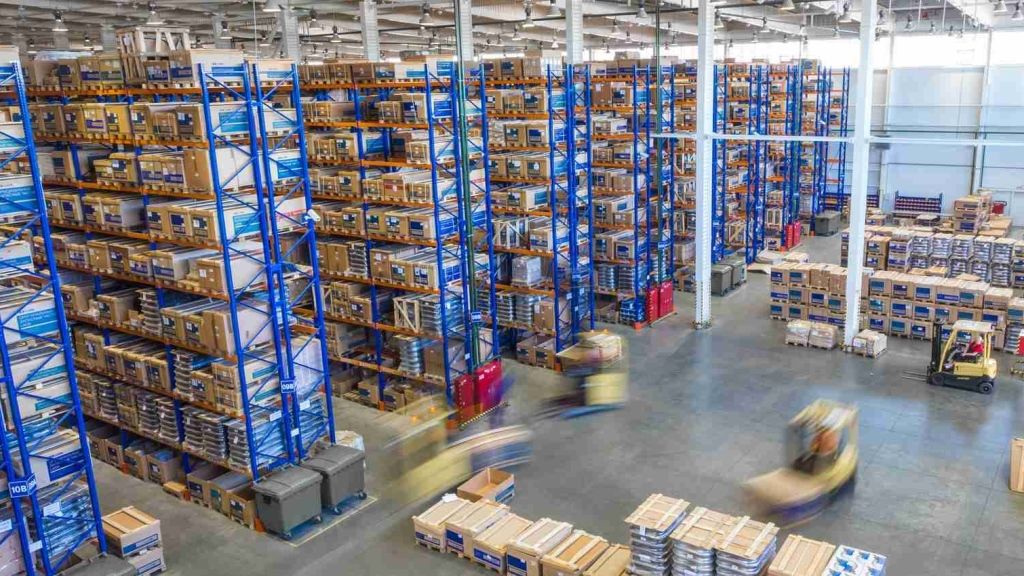
Simple warehouse design
The starting point for designing a warehouse system represents the process of designing logistics systems.
The design process consists of several phases: project identification, design process paradigm selection, system analysis, synthesis, and project evaluation.
This article’s contribution is the proposed methodology and design of the warehouse system for the specified conditions.
The methodology was implemented for the design of a warehouse system in a cold box, which is a part of a distribution warehouse.
The technology of pallet racking was chosen in the warehouse to store pallets. Pallets will be stored and removed by forklifts.
For the specified conditions, the warehouse system was designed for two alternatives of racking assemblies, which are served by forklifts.
- Alternative 1: Standard pallet rack with wide aisles and
- Alternative 2: Pallet dynamic flow rack.
Warehouse design systems
The proposed systems were compared on the basis of selected indicators:
- Capacity: the number of pallet places in the system
- Percentage ratio of storage area from the box area
- Percentage ratio of handling aisles from the box area
- Access to individual pallets by forklift
Warehouse operation process
Nowadays, thousands of tons of goods are transported from manufacturers to vendors and customers every day.
After freight is delivered to a vendor, it can be stored for a particular time in warehouses, where it waits for pick up. A warehouse is a place where multiple activities are carried out, depending on the warehouse function and position within a company’s logistics system or in its supply system.
Types of warehouse operations
Warehouses can be divided into two large types: distribution warehouses and production warehouses.
A production warehouse is used for the storage of raw materials, semi-finished products, and finished products in the production plant.
A distribution warehouse is a warehouse where products from different suppliers are collected (and sometimes assembled) for delivery to a number of customers.
Warehouse design requirements
Warehouse designing requirements result from their place and role in a logistics network. Warehouses are buffering (regulating) elements of supply chains, directing and transforming material flows. Apart from that, warehouses fulfill tasks, which add value to the products and increase their availability.
Warehouses also have a functional and technical side. The functional side is represented by the warehouse’s activities (the receiving of goods, control, storage, order-picking, accumulation and sorting, and shipping). The technical side consists of technical means ensuring material and information flow (racks, forklifts, hardware, software, etc.).
Warehouse design standards
The aim of this paper is to present one possibility of designing a warehouse system, where one of the principles of logistics is used: the system approach because the proposed warehouse system should be approached logically and systematically.
The systematic approach means that the processes and objects are visible and can be managed as a system.
The approach has been developed based on the experiences of a range of companies in a range of different business sectors.
Within the systematic approach, the warehouse system may be characterized as a part of the warehouse process.
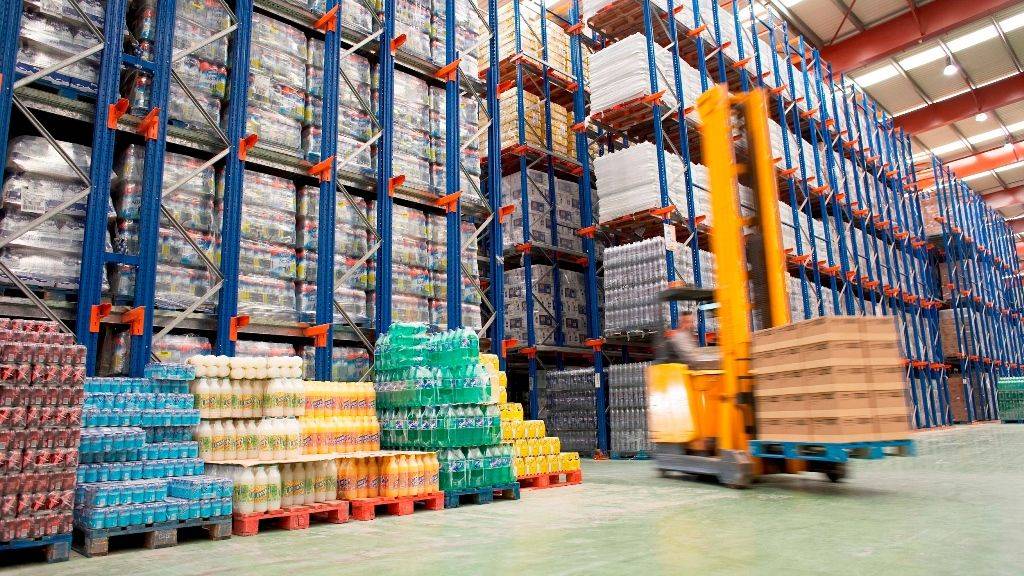
Warehouse system
The term warehouse system (WS) in this article means a system of two or more devices and means (storage and service equipment), forming a whole for the storage area, including their management.
The warehouse system’s composition depends on the chosen warehouse technology, and it consists of two basic parts: the racking assembly and the service equipment.
Choosing the right storage system is a topical research topic as it affects storage capacity and utilization, the speed of storage activities such as warehousing and removal, and operational safety.
The proposed methodology is a suitable tool for decision-making (e.g., for managers) in this area.

Warehouse Racking Design
The efficient, safe design and use of pallet racking storage systems, pallets, and materials handling equipment depend on a number of factors

Pallet Racking Types
Pallet racking is a material handling storage rack system designed to store products and materials on pallets in horizontal rows and on multiple levels.

Pallet Racking system
Selecting warehouse storage rack systems involves careful planning and appropriate system choices to ensure you get the most from your capital expenditures, reduce overhead, and respond quickly to distribution needs.
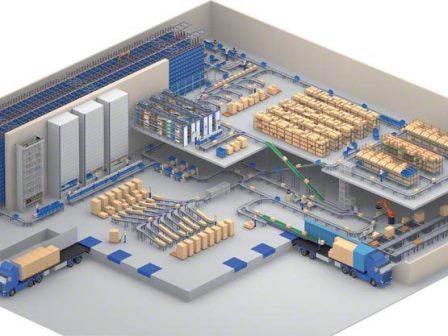
Warehouse Layout Design
With the continued growth and domination of e-commerce in the retail market, the demands on warehouses and distribution centers across the globe are also rising.