Safe operation of such cranes requires operators to have the knowledge and competence to avoid an accident, in addition to the overhead crane safe work procedure.
The purpose of this guide is to raise awareness of the hazards in lifting operations and to provide basic knowledge in the safe operation of overhead traveling cranes, gantry cranes, jib cranes, and hoists.
This guide is intended to be used by crane operators and supervisors to promote safe lifting operations in the handling of Overhead Travelling Cranes, Gantry Cranes, Jib Cranes, and Hoists.

OSHA overhead crane
A person conducting a business or undertaking has the primary duty to ensure, so far as is reasonably practicable, workers and other people are not exposed to health and safety risks arising from the business or undertaking.
This duty requires the person to manage risks by eliminating health and safety risks so far as is reasonably practicable, and if it is not reasonably practicable to eliminate the risks, by minimizing those risks so far as is reasonably practicable. It also includes ensuring so far as is reasonably practicable the:
- provision and maintenance of safe plants including cranes, and
- safe use, handling, storage, and transport of the plant.
The Work Health and Safety (WHS) Regulations include specific duties for a person conducting a business or undertaking with management or control of the plant, powered mobile plant, and plant that lifts or suspends loads.
If you own a crane you are the person with management or control of that plant.
If you hire or lease a crane, you have management or control of that plant for the period you have hired it. Both you and the person you have hired or leased it from will have duties to eliminate or minimize the risks associated with the plant, so far as is reasonably practicable.

Overhead crane risk assessment
risk assessment checklist
Find out what could cause harm. The following can help you identify potential hazards:
- Observe the workplace to identify areas where cranes operate and how they interact with other vehicles, pedestrians, and fixed structures like overhead electric lines.
- Ask the crane operator, crane crew, and others about problems they encounter at the workplace including operation, inspection, maintenance, repair, transport, and storage requirements.
- Review your inspection, test, and maintenance records e.g. logbooks, and incident and injury records including near misses.

Hazard assessment checklist
Assess the risk: In many cases, the risks and related control measures will be well known. In other cases, you may need to carry out a risk assessment to identify the likelihood of somebody being harmed by the hazard and how serious the harm could be. People who work with or near cranes are most at risk. Some of the risks when using a crane include:
- structural failure, overturning, or collapse of the crane
- contact or collision of the crane or its load with people or other plants and structures, and
- falling objects.
A risk assessment can help you determine what action you should take to control the risk and how urgently the action needs to be taken.
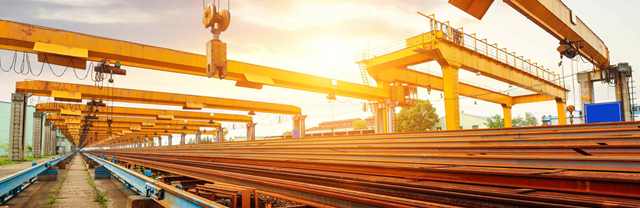
Risk management checklist
Take action to control the risk. The WHS laws require a business or undertaking do everything reasonably practicable to eliminate or minimize risks.
- The ways of controlling risks are ranked from the highest level of protection and reliability to the lowest.
- This ranking is known as the hierarchy of risk control. You must work through this hierarchy to manage risks.
- You need to consider possible control measures and make a decision about which are reasonably practicable for your workplace.
- Deciding what is reasonably practicable includes the availability and suitability of control measures, with a preference for using substitution, isolation, or engineering controls to minimize risks before using administrative controls or personal protective equipment (PPE).
- Cost may also be relevant, but you can only consider this after an effective review of all reasonably practicable control measures.
The first thing to consider is whether crane-related hazards can be completely removed from the workplace. For example, designing items of size, shape, and weight so they can be delivered, handled, or assembled at the location where they will be used without the need for a crane.
Event risk management checklist
If it is not reasonably practicable to completely eliminate the risk then consider the following options in the order they appear below to minimize risks, so far as is reasonably practicable:
- substitute the hazard for something safer e.g. replace a crane operating cabin with a restricted field of vision with one that has a clear field of vision or use a remote control, for example, a pendant control.
- isolate the hazard from people e.g. use concrete barriers to create an exclusion zone to separate crane operations from workers and powered mobile plant, and
- use engineering controls e.g. enclosing the operator with a falling objects protective structure (FOPS) to minimize the risk of the operator being hit by a falling object.
If after implementing the above control measures a risk still remains, consider the following controls in the order below to minimize the remaining risk, so far as is reasonably practicable:
- use administrative controls e.g. schedule crane operations to avoid or reduce the need for pedestrians and vehicles to interact with the crane in the area of operation, and
- use PPE e.g. gloves, hard hats, high visibility vests, earplugs/muffs, and eye protection.
Check your control measures. Control measures need to be regularly reviewed to make sure they remain effective, taking into consideration changes, the nature, and duration of work, and that the system is working as planned.

Occupational health and safety procedures
Who is involved?
You must consult your workers and their health and safety representatives if any when deciding how to manage the risks of using a crane in the workplace.
If there is more than one business or undertaking involved at your workplace you must consult them to find out who is doing what and work together so risks are eliminated or minimized so far as is reasonably practicable.
This may involve discussing site-specific requirements including the type of crane to use, operator training, and traffic management.
Further information on consultation requirements is in the Code of Practice: Work health and safety consultation, co-operation and co-ordination.
Overhead crane safety checklist
Before using a crane
The person with management or control of the plant at a workplace must ensure, so far as is reasonably practicable, the plant used is specifically designed to lift or suspend the load. A crane is one type of plant generally designed to especially lift and suspend loads.
The type of work you will be doing, how it will be done, and who will be involved should be planned and discussed between the people involved in the work before deciding what type of crane will be used.
This includes people directly, for example, crane operators and other workers, and indirectly, for example, suppliers, designers, and crane hirers involved with the work.

Choosing a crane
Before you choose a crane you should discuss your workplace needs with suppliers and identify the cranes most suited to the workplace and the work for which they will be used.
Take into consideration the complete life cycle of the crane, how long you are likely to keep the crane, how often the crane is likely to be used, the conditions under which it will be used and the maximum loads the crane is likely to bear.
A second-hand crane is more likely to have outdated or missing safety features. Suppliers of second-hand cranes must do what is reasonably practicable to supply equipment that is safe to use at work and where practicable, fits safety features.
Some of the things to look for when choosing a crane are:
- safe access points e.g. ladders, footholds, steps, and grabs rails
- seat design e.g. comfort and back support
- visibility e.g. mirror, window, and windscreen design, and
- environmental controls e.g. temperature control units to avoid worker heat stress
Hiring a crane
Anyone hiring or leasing a crane to others has duties as both a supplier of the crane and as a person with management or control of the crane at the workplace. They must check the crane is safe to use and properly maintained and provide specific information with the crane including instructions on how to operate it safely.
Before you hire a crane you should check it is suitable for its intended use. You should also consider whether you need to hire a crane only or a crane with a trained and licensed crane crew.
If you do not have the knowledge or expertise about crane specifications, limitations, and operational requirements, you should talk to the crane supplier and provide relevant information about the work to be done, the workplace and the type of lifts to be completed so the supplier can provide a suitable crane.
Registering a crane
Some cranes must be registered before they can be used in the workplace. Cranes that are registrable plants must be designed and registered before they are supplied and used. Further information on registration requirements can be provided by the regulator.
More information on registrable plants including cranes is in the Code of Practice: Managing the risks of plant in the workplace.
Overhead crane inspection checklist
Inspection and pre-use safety checks. Inspecting and testing for cranes must include the:
- major inspection required for registrable mobile and tower cranes
- regular inspection and testing are required for plant, and
- inspection and testing for plant item re-registration.
Further information on crane inspection and maintenance is in the Guide to inspecting and maintaining cranes.
Before a crane is used, tests, inspections, and specific adjustments must be undertaken to ensure the crane can be used safely. This includes:
- workplace factors including ground load-bearing capacity, and wet or windy conditions are taken into account
- to confirm the crane will not adversely affect or be affected by other plants and structures in the area
- installation and commissioning activities are supervised by a competent person
- the components are assembled in the correct sequence using the right tools and equipment
- limit switches and load indication devices are functioning and correctly calibrated
- the crane has been installed and commissioned to the designer’s or manufacturer’s instructions and specified technical standards
- the crane is stable, and
- safe entry to and exit from the crane—including in an emergency
Emergency plan
An emergency plan must be prepared for each workplace where the crane will operate. The plan must be tested in the workplace and include emergency procedures like effective response and evacuation, notifying emergency services and medical treatment. Emergency procedure training must be provided to workers.
Contact numbers for emergency services should be easily seen or found. Workers should know what system is in place to contact emergency services and how to use it.
- Rescue equipment should be available and easily accessible so an injured worker including the crane operator can be removed quickly.
- Signs displaying evacuation locations should be placed where they are easily seen by workers and others at the workplace.
- The emergency plan should also include how these procedures will apply to people who are near the crane as well as those people who are operating the crane (e.g. procedures for evacuating the workplace).
Crane setup procedure
Setting up and operating a crane: Documentation and markings.
Crane capacity chart
Load charts
A crane of variable radius, for example, a tower or mobile crane, will have a crane-specific load chart (also known as a ‘rated capacity chart’) setting out how the crane lifting capacity varies depending on how the crane is set up i.e. how far the boom is extended and the angle of the boom. Using the load chart correctly is critical to ensure the crane is used safely.
Where the crane has one main load chart it should be fixed in the operator’s cabin in a place that is easy to see and read. Where the crane has more than one load chart, for example for different boom and fly jib configurations, the charts should be easily accessible for the operator to verify the crane will not be overloaded. The charts may be kept electronically or in hard copy.
The lifting capacity of a crane is generally limited by:
- structural strength when the working radius is small
- stability when the working radius is greater.
Structural limits
However, there are structural limits at both the minimum and maximum working radius. If a crane is overloaded, a structural or mechanical component of the crane may fail or the crane may overturn.
The lifting capacities specified on a load chart should not be exceeded except during testing of the crane by a competent person under controlled conditions. Each load chart should include enough information to identify the crane configuration it applies to. For example:
- the safe working zone
- the counterweight mass
- whether a fly jib is fitted, in use, in place or stowed
- outrigger extension or pick-and-carry mode
- maximum speed for mobilizing a load
- rope and reeving details, including the number of falls of rope in the hook block
- main or auxiliary hoist in use, and
- whether the hook block is included or excluded.
crane load chart
Some important factors which are often overlooked when reading load charts are:
- Subtracting the mass of the hook block and lifting slings from the capacity of the crane at the particular radius. This should be noted on the load chart. For example, if the load chart states the crane can lift 20 tonnes at a given radius but the hook and lifting gear have a combined mass of 1 tonne, the load to be lifted cannot be more than 19 tonnes. This issue is critical for heavier hook blocks and lifting gear, for example, spreader beams.
- Subtracting the mass of the fly jib (adjustment mass) from the capacity of the main hook when lifting from the main hook on the main boom with a fly jib attached to the boom head. This adjustment mass should be noted on the load chart—there may be two different masses for some cranes with a swing around fly jibs—one for the fly jib in place and another for the stowed position. Capacities of the main boom are generally based on the fly jib being removed. If this issue is ignored, the crane is likely to overturn.
- The increased maximum working radius that may result when using a fly jib
Overhead crane operator
Limiting and indicating devices.
Limiting and indicating devices, for example, rated capacity limiters, the motion limiting devices, load indicators and radius indicators are intended to prevent a crane moving beyond its safe operating limits or to aid crane operators. The devices should not be relied on in place of using the crane’s load chart and operating instructions. Sole reliance on these devices, especially indicating devices, in place of safe operating practices may cause an incident.
Where limiting and indicating devices are to be installed on a crane the safety circuits of these devices should generally meet either:
- a reliability level of Category 4 under AS 4024.1-2006: Safety of machinery
- a safety integrity level (SIL) of 3 under AS 61508-2011: Functional safety of electrical/electronic/programmable electronic safety-related systems.
These categories of reliability level and SIL are related to the concept of ‘fail-safe’.
OSHA lockout Tagout
Freefall lock-out: When a crane is fitted with a free fall facility this function should be able to be positively locked out and not able to be unintentionally activated.
Is overhead crane training required OSHA?
While OSHA standards do not spell out overhead crane training requirements, the American Society of Mechanical Engineers does get much more specific in the ASME B30.2 standard. It further states that a company’s management is responsible to “provide training to persons who will operate a crane”
A crane is an item of a plant intended for raising or lowering a load and moving it horizontally including the supporting structure of the crane and its foundations. There is a range of ‘fixed’ (tower, bridge, gantry, portal boom, vessel-mounted) and ‘mobile’ (slewing, non-slewing, vehicle loading) cranes. A range of multi-purpose powered mobile plant including multi-purpose tool carriers and telescopic handlers may be classed as cranes in some operating configurations.
The three most common hazards involving overhead cranes include electrical hazards, overloading, and materials falling/slipping from overhead hoists.
Under the act, all employers have a duty of care to their employees which includes:
To eliminate risks to health and safety so far as is reasonably practicable; and if it is not reasonably practicable to eliminate risks to health and safety, to reduce those risks so far as is reasonably practicable.
This requires an employer to so far as is reasonably practicable, provide and maintain for employees of the employer a working environment that is safe and without risks to health. This includes the provision of such information, instruction, training or supervision to employees of the employer as is necessary to enable those persons to perform their work in a way that is safe and without risks to health. The act also requires that a person must not carry out work, or an activity if the regulations require the work or activity to be carried out by a person who is registered or licensed.
The most read

Overhead Cranes
What are the parts of an overhead crane? What is the purpose of an overhead crane?

Overhead Crane Test Questions and Answers
Crane operator interview questions and answers. Rigging test questions and answers

Overhead Crane Safe Work Procedure
What overhead crane operators always need to keep in mind is that they are responsible for the safety of other people.